The Fixers - Wood Stoves
Wood stoves and more
By Greg Rössel
Illustration by Caroline MagerlIt’s easy to forget, in these days of pricy imported fuel, that not all that long ago a good part of Maine was energy self sufficient – burning locally grown wood in locally built stoves. And while some homeowners opted for imports from distant places like Vermont or Taunton, Massachusetts, there were also many homegrown heaters and ranges: the “Atlantic” from Portland Stove Foundry, the ubiquitous “Clarion” from Wood and Bishop of Bangor, the “Kineo” from Noyes and Nutter (also of Bangor). Or for that matter, the stove might have been built in Waterville, Houlton, Mapleton, Hampden, Augusta, or Brunswick. It seemed that almost anywhere you went in Maine you might find a stove foundry.
Part household appliance, part furniture, the cast iron range and parlor heater was a study in practical and elegant construction. Some have likened a cast iron wood stove to a steam locomotive: levers and dampers that slide, lids that lift, shakers that shake, heat chambers and flues, water jackets, and dandy thermometers.
One was expected to know one’s woods (and their relative heating values) and to be an active participant in the heating and cooking process. Like any proper locomotive of the same period, a wood stove would have ornamentation ranging from humble to elaborate. Nickel plated trim was common and the cast iron would be adorned by foundry men with bas relief scroll work in Gothic, Greek, Italianate, Rococo, or Egyptian motifs. There might be cast-in lion’s heads, a cod fish, a quote from Milton, or even torch-wielding cherubs traipsing through a vineyard accompanied by a hound. There could be iron urns that humidified, stacks that recalled temple columns, warming ovens and swinging elevated trivets. The entire top of the kitchen range was a cooking surface of differing temperatures. Some had ovens that could accommodate a 35-pound Thanksgiving turkey — and all the trimmings. Also reflecting the era, the devices bore confident names: “Queen Atlantic,” “Star Kineo,” “Home Comfort,” “Glenwood Oak,” “Monitor,” “Hot Blast,” and “Climax.” Clearly these were appliances to be reckoned with.
Alas, times change. Wood heat went to central heating. Gas and electric ranges arrived in kitchens. No stove black, firewood, or ashes to contend with. Just turn it on and there you go. Many of the old stoves were broken up. But others simply went into retirement in the barn or shed to await better times. These arrived in the early 1970s when a fuel crisis and a back-to-the-land movement rekindled an interest in the practical business of wood heating.
By this time, most of the old foundries were gone, but the remaining old stoves could be dusted off, and with the addition of some new grates and perhaps a few parts, they would be ready to go. If, that is, you could find the stoves -- and the parts. Enter Bea and Joe Bryant.
In downtown Thorndike is the home of Bryant Stove and Music Inc. There, Bea and Joe specialize in restored antique stoves — kitchen and parlor, Franklin, wood/gas combination, and gas. Also, they will restore customer’s individual stoves, supply hard-to-get parts and offer nickel plating. A visit to the showroom is akin to a stop at an antique car museum. Polished black iron (and occasional enamel) is accented by glistening nickel. Cook stoves in a wide array of sizes jostle with parlor heaters of all sorts.
(The Fixers - Wood Stoves cont.)
photo by Greg Rossel
Bea Bryant started her wood stove restoration business in the late 1960s. “I just liked them” she said. “And Joe had the shop that could do the work.” Cast iron stoves can last more than a lifetime and a 90-year-old cook stove left in place with a kerosene burner can still be just like new. But, continuous exposure to hardwood fires can burn and warp metal, stove cement can fall out, and abuse or simply moving the heavy devices can damage parts.
Stoves have to be re-built to at least the same quality as the original. Joe outlined the process: ”Someone will bring in a stove. We have two men who go over the stove and determine the price to restore it. First, we cut every bolt, disassemble the stove and put it into a shopping cart and we take it to the Wheelabrator machine that cleans the pieces by slinging metal shot at it. One pass through the machine usually does it.” They also have a sandblaster for larger pieces
Tracking down parts has been more problematic. Noted Bea, “It was hard for us when Portland (Stove Foundry) went out in the mid 1980s. One by one, the foundries in the east had to close.” As each foundry closed there was always the chance the delicately elegant carved wooden patterns might be lost forever. When Noyes and Nutter shuttered their doors, their “Kineo” patterns were sold to Wood and Bishop. When they ended their run in 1939, the Portland foundry acquired both sets. Finally, in 1982, the Bryants purchased all those just as Portland was closing.
Said Joe, “The original patterns are best but in a pinch, you can use an old part for casting but you have to deal with a small amount of shrinkage.”
Today, some iron parts are cast at a small foundry in Maine, while others are fabricated in the midwest. Nickel plating is also done out-of-state. Currently, the Bryant’s have most of the critical parts for a Maine-built stove and many parts can be adapted to fit stoves from away. Right now, they are probably the only ones in the state stocking new parts.
What can’t be found new, can likely can found out back. Said Bea, “We buy (non-rebuildable) stoves on purpose just for parts. We have quite a junkyard.”
After the parts have been cleaned, welded if necessary, and new ones obtained, the stove is reassembled with the same care as when it was new. It’s then carefully painted, the nickel trim added, and the finished product is brought out to the showroom. “Business has gotten better every year,” observed Joe. “People come from all over the world – England, Alaska, Germany. Several of our stoves have gone to Disney World and other museums.”

Bryant Stove and Music Inc. can be found at 27 Stovepipe Alley (located at the junction of Routes 139 and 220), Thorndike, ME 04986. 207-568-3665; www.bryantstove.com
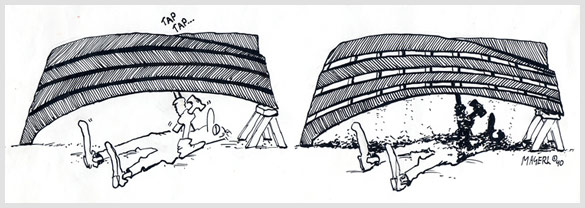
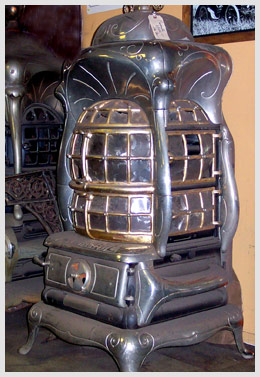
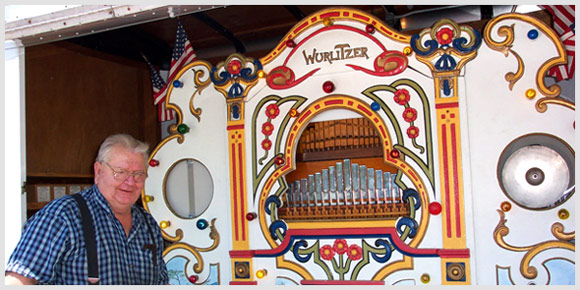

Calliopes and band organs
Next door to the Bryant’s stove showroom is the museum of really old stoves (1750 to 1850), antique cars, operating toy engines of all sorts, a wonderfully quirky doll circus (with its leather–clad flying bear in a biplane, a Barbie doll fashion show driven by hidden bicycle sprockets and chain, and a magnet-drive toy auto route) and an operating full-size carousel horse. But perhaps, best of all in this musée mecanique is the mechanical music department. This is perhaps Joe Bryant’s favorite area of restoration.
Said Joe from behind the keys of a player piano, “When I was in high school at Freedom Academy, there was an old player piano. I was fascinated with it and even though there were no music rolls, I would pump the pedals just to see the machinery go.”
What was probably the catalyst for collecting and restoring these instruments was one trip Joe and Bea took though Aroostook County in search of stoves. They came upon a fellow who had a player piano for sale, and that began the collection of barrel nickelodeons; Edison record players; hurdy-gurdys; crank roller organs with reeds like a harmonica; transitional music machines that, by swapping out discs, could either be a music box or record player; a portable organ for old time revivals; a coin-operated Wurlitzer; a player accordion; a motion-picture sound-effect player; and a piano player that actually plays the keys of a standard piano.
Continued Joe, “Calliopes and band organs have an altogether different sound but are often confused. Calliopes, with their forest of pipes on top, brought people to the circus when it came to town. Band organs are those often seen on carousels and had wooden pipes. There is quite a bit of work to bring these instruments back. We take them apart and reassemble them just like we do the stoves. The player pianos take hours and hours to restore”.
While there might seem to be quite a spread among cast iron stoves, antique automobiles, and player pianos, there is a constant connecting thread: Bea and Joe Bryant appreciate the ingenious machinery of the past and love restoring it to do the job it was originally intended to do. |
Related Articles
Share this article:
2023 Maine Boat & Home Show
Join Us for the Maine Boat & Home Show!
Art, Artisans, Food, Fun & Boats, Boats, Boats
August 11 - 13, 2023 | On the waterfront, Rockland, Maine
Click here to pre-order your tickets.
Show is produced by Maine Boats, Homes & Harbors magazine.