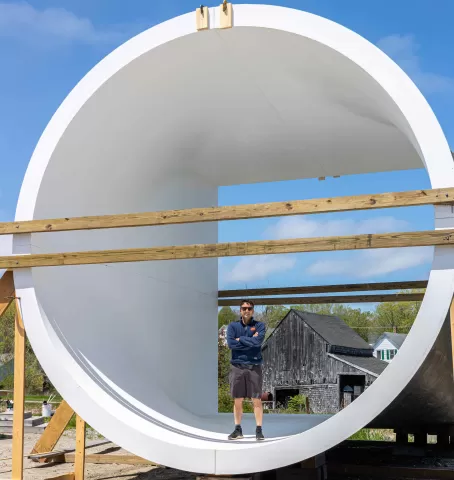
Latest Lyman Morse Launch? A wind tunnel
Talk to Drew Lyman about the future of his boat-building business and how Lyman Morse has fared in the current economic upheaval, and he will tell you how proud he is of the company's success at diversifying and finding new applications outside the marine world for its boat-building expertise. That diversification helps cushion the impact when orders slow in any one area.
“It’s a logical thing,” says Lyman, president of Lyman Morse, which is based in Thomaston and also operates the former Wayfarer yard in Camden. “We can apply the technology we use in building high-end boats in other projects.”
A recent example is a 16’x 30’ composite wind tunnel. Lyman-Morse Technologies, the company’s research, development and prototyping division, won the contract from a specialist manufacturer in the business of designing and providing custom wind tunnels to customers all over the world. This tunnel is destined for a major academic research facility on the East coast of the United States. Among its many aerodynamics functions, the tunnel will be used to support aerospace research projects.
“Given the many advanced skills and trades needed to build a world class custom yacht, technology, defense and aerospace firms recognize the value in what we do. This was an exciting win for us and we hope to be doing more of these,” said Andy Smith, Vice President of Lyman-Morse Technologies.
Steve Crane, composite division manager, and his team approached the wind tunnel project as they would any boatbuilding project. Inhouse designers used 3D modeling software to finalize the design and engineering data. This data was inputted into Lyman-Morse’s CNC machine to cut the mold frames to the exacting tolerances required for the intended performance of wind tunnel. As in boatbuilding, the composite team built a mold, and laid in the composite layers. In this particular case, the parts were made in quadrants from male molds which create the inner surface of the wind tunnels. To finish the inner surface, the inside of the tunnels includes a layer of gelcoat. When assembled the wind tunnel will be 30’ long with a 16’ diameter.
"Whether building a church steeple for the town of Camden, producing a Radome prototype, executing projects for the Department of Defense, or designing and building an automated boathouse door, boat cradle and controls for a marine railway, LMT has been sought out for their clean technology, precision and hi-tech capabilities utilizing advanced composites,” said Lyman. “We thrive on this kind of work.”
Drawing on Thomaston, Maine’s 200-year tradition of shipbuilding and craftsmanship, Lyman-Morse is a custom and semi-custom builder of and service provider for sailing and motor yachts. A family run business, Lyman-Morse specializes in composites, advanced composites and aluminum construction. Since the yard’s founding in 1978, more than 100 yachts have been sent down the St. George River ranging in scope from carbon fiber catamarans and traditional sailing sloops to not-so traditional carbon racing monohulls, motor yachts and sportfish powerboats to jet boats and daysailers.
The 11-acre Thomaston campus features 7 heated work buildings with 55,000 square feet of space for refit and repair/and boatbuilding. Lyman-Morse’s Camden yard is at the site of the former Wayfarer Marine. The company has brokerage offices in Camden and Northeast Harbor, Maine and Newport, Rhode Island.